建立180L/s 螺杆真空泵转子温度场有限元模型,得到其温度场和热形变分布情况,结合热形变结果推导出泵腔内各点冷配合间隙。利用分析结果对螺杆真空泵转子形状进行优化设计。分析结果显示:180L/s 螺杆真空泵两转子之间间隙应大于0.28mm,泵腔和转子之间间隙应大于0.20mm。结合所述分析结果对转子形状进行优化,优化后的转子可以减少原有22%冷配合间隙,一定程度上降低泵工作过程中返流量。螺杆真空泵转子的装配间隙取决于工作状态下转子每一个啮合位置的热形变量。工作状态下转子径向热形变量较大,需要预留一定装配间隙,这些间隙很大程度上影响了泵的抽气性能。环境温度较低的工况下,工作前需要对螺杆真空泵进行预热,使转子膨胀一定程度以弥补较大的冷配合间隙,泵才能正常工作。很多学者曾对螺杆真空泵转子型线和转子热形变情况进行研究,为螺杆真空泵转子型线和热学分析做出许多贡献。本研究对螺杆真空泵转子进行热形变分析,并结合分析结果对转子曲线的轴截面形状进行优化设计,一定程度上减少了转子的装配间隙。
1、有限元模型的建立选择180L/s 螺杆真空泵作为研究对象,其几何参数如表1 所示。建立主动、从动转子的简化三维模型。转子端面型线如图1 所示。
表1 螺杆泵转子几何参数
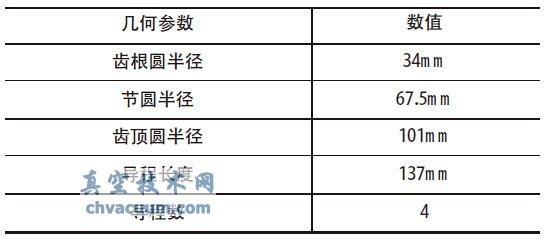
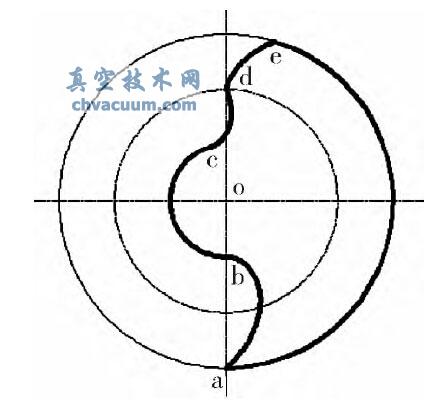
图1 转子型线方程
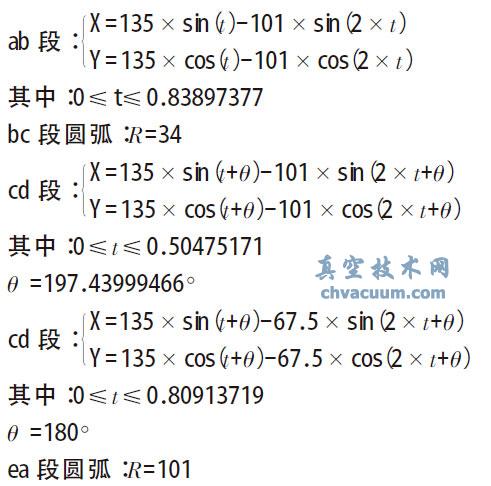
将模型导入有限元分析软件。热分析涉及的三维实体单元有SOLID87、SOLID70 和SOLID90,选择20 个节点的分析单元类型SOLID90。因不锈钢螺杆难以加工,目前大多数螺杆真空泵转子材料采用铸铁,其物性参数如表2 所示。考虑到螺杆转子的几何形状较为复杂,对转子进行自由网格划分,得到螺杆真空泵转子的有限元模型。
表2 转子物性参数
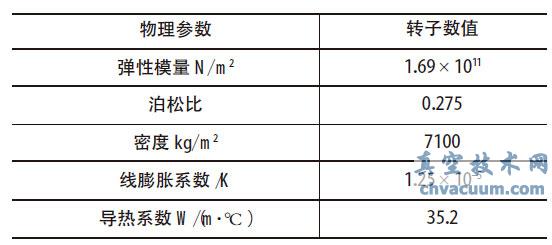
2、热载荷的施加2.1、热边界条件的选取
进行热分析之前,需要确定单值性条件,包括几何参数、物性参数和边界条件。几何参数和物性参数上文已经给出。边界条件的选取是单值性条件的关键。
热学分析边界条件有三类,本文采用施加第三类边界条件,即施加转子接触的流体介质温度和对流换热系数。根据转子运转过程中每一级封闭腔流体介质状态不同,转子热边界条件按照导程划分为四部分。
2.2、边界条件的确定
螺杆真空泵工作过程中所产生的热量主要来源于最后一级运输腔压缩气体做功。最后一级运输腔涉及到的热力学表达式为:
Q-W=ΔU (1)
式中:Q 为最后一级运输腔与外界交换的热量;W 为对外所作膨胀功;ΔU 为热力学能变化。由文献中转子温度的实验结果可知,转子前三段温度每一级温度可近似为线性分布。螺杆泵工作时的气体运输可以近似为管道流动过程,故选择管内受迫流动准则方程确定传热系数。
Nu=0.023Re 0.8 Pr 0.3 (2)
式中Nu 为努塞尔数;Re 为雷诺数;Pr 为普朗数。
反映对流换热强弱的努塞尔数公式为:
Nu=ad/λ (3)
式中a 为对流换热系数;d 为当量直径;λ 为流体的导热系数。
由式(2)和(3)联立可得
a=0.023Re 0.8 Pr 0.3 d/λ (4)
根据每一级不同流体状态,得到阴阳转子的对流换热系数和当量温度。
3、分析结果3.1、温度场分布
本研究分析的是所抽气体温度为30℃,螺杆真空泵正常工作时的稳态温度场分布。将计算得到的边界条件施加在转子表面,得到主、从动转子温度场分布如图2 所示。
从图2(a)、(b)可以得知主动转子和从动转子的温度沿轴向从进气端至排气端逐渐增高。主动转子的进气端为112.50℃, 排气端温度为179.57℃;从动转子的进气端温度为110.65℃,排气端温度为178.46℃。
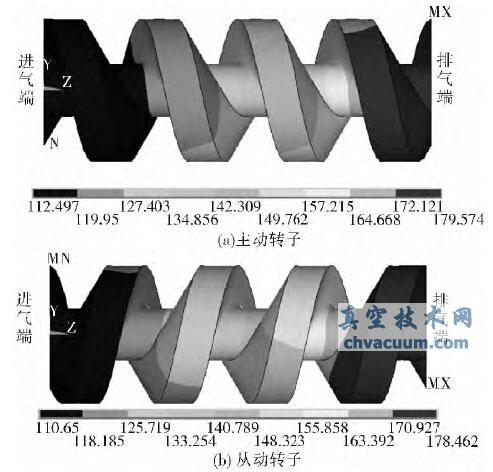
图2 转子温度场分布云图
3.2、热形变分析
基于温度场分析结果求得转子热形变量。图3 显示了转子工作状态下齿顶圆、齿根圆径向热形变量大小。由图可知,齿顶圆、齿根圆径向热形变量从进气端至排气端逐渐增大。齿顶圆最大热形变量为0.198mm,最小热形变量为0.078mm;齿根圆最大热形变量为0.074mm,最小热形变量为0.03mm。
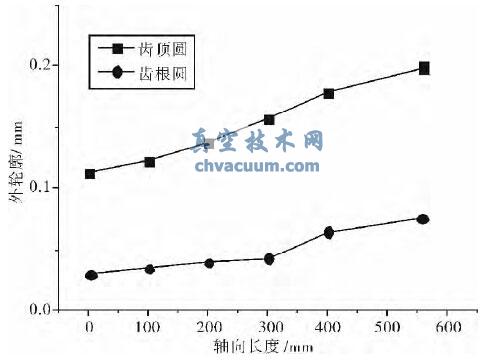
图3 转子各点径向热形变量
如果不考虑转子端面间隙,泵腔内存在四处间隙,α 处为一个转子齿顶圆与另一个齿根圆的间隙,β 处为两转子型线中cd、de 段之间的间隙,γ 处转子齿顶圆与泵腔之间间隙,ε 处为两转子型线中ab 段之间的间隙,如图4 所示。转子的齿顶圆与另一转子的齿根圆啮合,通过图3 齿顶圆与齿根圆径向热形变曲线可以确定α 处间隙值应该不小于0.28mm。由于两转子轴向热形变量差别不大,一般不考虑转子热形变量对两转子轴向间隙的影响。工作状态下泵腔热形变量很小,所以γ 处泵腔与齿顶圆间隙可由齿顶圆热形变量决定,应该不小于0.20mm。α 处间隙与两转子轴向间隙值确定后间接可以推断出β和ε 处装配间隙值。
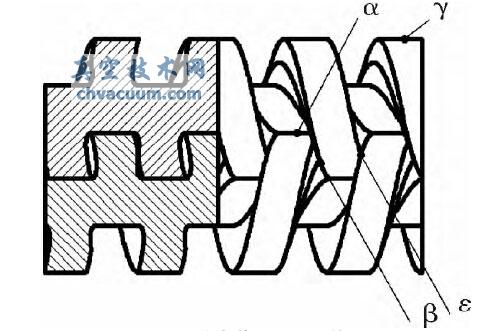
图4 泵腔内装配间隙带位置
4、优化设计针对转子各点径向热形变量存在的差异,从转子形状入手,加工转子时对其热形变量大的位置进行切削,提前预留出工作过程中转子热形变对间隙的补偿值,达到减小装配间隙的目的。通过分析结果可以看出转子径向热形变量从进气端至排气端呈线性递增,因此优化思路为加工转子时将整个转子外形做成锥形,进气端较粗,排气端较细,真空技术网(http://www.chvacuum.com/)认为可以一定程度上减小两转子之间的冷配合间隙,降低泵工作过程中的返流量,达到提高螺杆真空泵的抽气性能的效果。型线的特征为转子ab 段于另一转子的a 点啮合,转子cd 段和另一转子的e 点啮合,de 段和另一转子的d 点啮合。e 点在齿顶圆上,d 点在节圆位置上。
因此优化设计的方案是将粗加工好转子的齿顶圆切削量从进气端的0mm 线性增大至排气端的0.12mm,使得加工出的转子外圆成锥形,并将端面型线方程上d 点对应的那条螺旋线打磨掉0.05mm。装配时排气端齿顶圆与齿根圆之间间隙取排气端齿顶圆与齿根圆最大热形变量之和,为0.28mm,此时进气端齿顶圆与齿根圆之间间隙为0.16mm。装配时排气端齿顶圆与泵腔之间间隙取齿顶圆进气端径向热形变量,为0.2mm, 此时进气端齿顶圆与泵腔之间间隙为0.08mm。这样以来装配位置α、γ 处均不会发生干涉,由于转子cd 段和另一转子的e 点啮合,de段和另一转子的d 点啮合,e 点在齿顶圆上,齿顶圆经过切削处理,d 点打磨掉0.05mm,因此ε 处不会发生干涉,a 点也在齿顶圆上,同理β 处间隙也不会发生干涉。确定理论装配间隙的平均值如表3 所示。
表3 装配间隙平均值大小对比
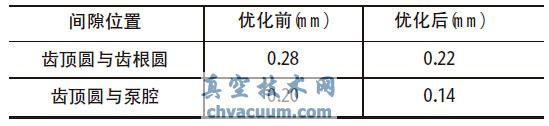
由文献可知,影响螺杆真空泵返流量主要因素为齿顶圆与泵腔的间隙,其返流量计算公式为:
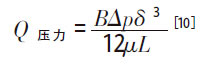
其中B 为缝隙长度;Δp 为缝隙前后压差;δ为缝隙宽度。将表3 优化前与优化后的间隙值带入返流公式求得优化后的转子可以减少52%工作状态下齿顶圆与泵腔之间返流量。
5、总结对螺杆真空泵转子进行温度场和热形变模拟计算,得出转子泵腔内的冷配合间隙大小。结果显示转子齿顶圆与齿根圆之间装配间隙应大于0.28mm,齿顶圆与泵腔之间装配间隙应大于0.20mm。结合分析结果对转子方程形状进行优化设计。优化后齿顶圆与齿根圆间隙平均值减少为0.21mm,齿顶圆与泵腔之间间隙平均值减少为0.14mm。利用返流公式求得优化后的转子可以减少52%齿顶圆与泵腔之间返流量。